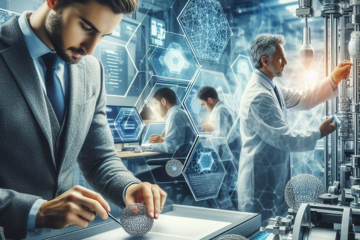
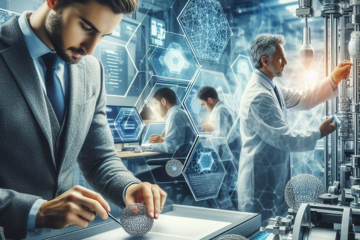
The Transformative Power of CAE
Introduction:
In the dynamic realm of mechanical engineering, innovation is the cornerstone of progress. From designing efficient engines to optimizing manufacturing processes, mechanical engineers are constantly pushing the boundaries of what’s possible. Enter Computer-Aided Engineering (CAE), a game-changing technology that is revolutionizing the field by providing engineers with powerful tools to simulate, analyze, and optimize mechanical systems. In this blog post, we’ll explore how CAE is reshaping the landscape of mechanical engineering, driving innovation, and propelling the industry forward.
The Role of CAE in Mechanical Engineering:
At its core, mechanical engineering is about designing and optimizing physical systems to meet specific performance criteria. Traditionally, this process involved a combination of theoretical analysis, physical prototyping, and empirical testing. While effective, this approach could be time-consuming, costly, and limited in scope. CAE, however, offers a more efficient and cost-effective alternative by allowing engineers to create virtual prototypes and conduct detailed simulations before any physical components are built.
Creative Problem-Solving:
At its core, engineering is about creative problem-solving. Engineers are like modern-day inventors, constantly seeking new ways to overcome obstacles and achieve objectives. They use mathematics, science, and technology as tools to turn ideas into reality, drawing inspiration from nature, art, and everyday life. Whether it’s designing a more efficient engine, optimizing a manufacturing process, or improving the user experience of a product, engineers approach challenges with curiosity, resourcefulness, and a willingness to experiment.
Applications of CAE in Mechanical Engineering: The applications of CAE in mechanical engineering are as diverse as the field itself. Whether it’s analyzing the structural integrity of a bridge, optimizing the aerodynamics of a vehicle, or simulating the flow of fluids through a heat exchanger, CAE enables engineers to tackle a wide range of design challenges with unparalleled precision and accuracy. Some common applications of CAE in mechanical engineering include:
Structural Analysis: CAE tools such as finite element analysis (FEA) allow engineers to simulate the behavior of mechanical structures under various loading conditions, helping to identify potential weaknesses, optimize designs, and ensure structural integrity.
Thermal Analysis: CAE can be used to model heat transfer phenomena, such as conduction, convection, and radiation, allowing engineers to optimize the thermal performance of mechanical systems and components.
Fluid Dynamics: CAE tools like computational fluid dynamics (CFD) enable engineers to simulate the flow of fluids and gases through complex geometries, helping to optimize the design of pumps, valves, and HVAC systems.
Mechanism Design: CAE software can be used to simulate the motion and behavior of mechanical systems, such as linkages, gears, and cams, allowing engineers to optimize performance, reduce vibration, and minimize wear and tear.
Benefits of CAE in Mechanical Engineering: The adoption of CAE offers numerous benefits to mechanical engineering organizations, including:
Faster Time-to-Market: By enabling engineers to rapidly iterate on design concepts and conduct virtual tests, CAE accelerates the product development process, reducing time-to-market and giving companies a competitive edge.
Cost Savings: CAE minimizes the need for costly physical prototypes and testing, saving time and money during the design and development process.
Improved Product Performance: Through detailed simulation and analysis, CAE helps engineers optimize the performance, durability, and reliability of mechanical systems and components, leading to better-performing products that meet or exceed customer expectations.
Enhanced Innovation: CAE provides engineers with insights and capabilities that were previously impossible or impractical to achieve, fostering innovation and pushing the boundaries of what’s possible in mechanical design.
Challenges and Considerations: While the benefits of CAE are significant, its adoption is not without challenges. Effective use of CAE requires specialized skills and expertise, as well as robust computational resources to handle complex simulations. Additionally, the accuracy of CAE results depends heavily on the fidelity of the underlying models and the quality of the input data. Despite these challenges, the potential of CAE to drive innovation and improve engineering outcomes makes it an indispensable tool for mechanical engineering organizations looking to stay ahead in today’s competitive marketplace.
Looking Ahead: As technology continues to advance, the capabilities of CAE are expected to grow exponentially. From advances in simulation algorithms and optimization techniques to the integration of artificial intelligence and machine learning, the future of CAE promises even greater efficiency, accuracy, and innovation in mechanical engineering. As organizations continue to embrace CAE as a fundamental part of their design process, we can expect to see increasingly sophisticated and impactful mechanical solutions that push the boundaries of what’s possible.